Ultrasonic testing and fault checking
Ultrasonic inspection by fault checking is an indispensable part to obtain quality control at the highest level.Measuring instruments for ultrasonic inspection
Ultrasonic inspection is part of non-destructive inspection and testing methods. Fault checking is carried out
by means of an acoustic procedure. A probe sends sound waves through ultrasound conducting materials in an
approximate frequency range between 500 kHz and 50 MHz. Ultrasound bounces where there are materials of
different density and wave impedance. These boundary layers are found, for example, in cavities, fissures…
These are determining factors that require a weld check.
By the transit time of the ultrasound
measuring, it's possible to determine the size and position of the fault in practically the entire piece. That
is why the ultrasonic inspection for fault checking mainly serves for the control of metal parts in the
different industrial sectors, for the verification of welds and materials and for the control of semi-finished
products. It can be used to measure the thickness of a material, the hardness or the flow of a pipe
Weld inspection / Fault checking
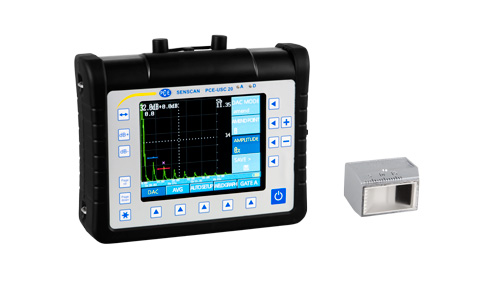
The inspection of welds with an ultrasonic meter allows non-destructive detection of cracks, inhomogeneities in the material (steel, stainless steel, aluminum). Thanks to the inspection of welds and verification of faults by ultrasound, you can perform a quality control cash
Measurement of hardness by ultrasound
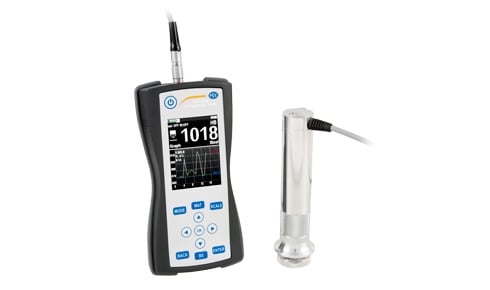
The measurement of the surface hardness of a material is an important area of ultrasonic inspection. The UCI (Ultrasonic Contact Impedance) procedure allows a non-destructive test to be carried out directly on the material itself or on the finished product. PCE Instruments offers versions of this equipment for almost every type of application.
Ultrasonic thickness measurement
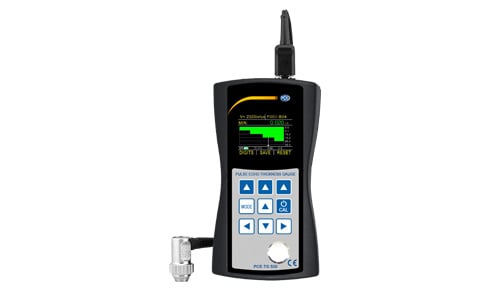
Ultrasonic measurement to accurately determine the thickness of a material is one of the most common measurement procedures for ultrasonic testing. PCE Instruments manufactures measuring instruments that measure in a range between 0.50 and 500 mm. Thanks to this, the measurement of material by ultrasound is simple, fast and very precise.
Ultrasonic flow measurement
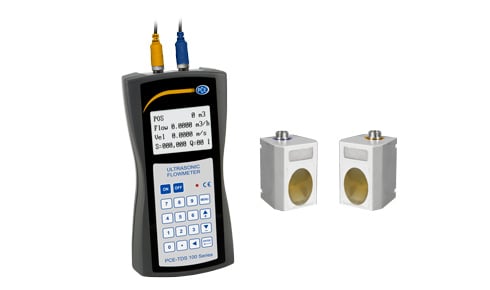
Ultrasonic flowmeters reliably and accurately determine the speed and flow in metal, plastic or rubber pipes, without the need to drill holes in the ducts and without interrupting the flow. PCE Instruments offers equipment to measure the flow rate by ultrasound with different configurations so that they adapt to all types of pipes.
Training courses
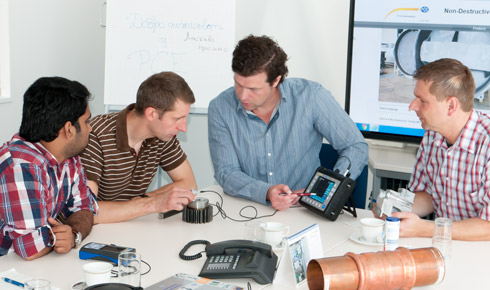
Practical team training courses.
All instruments for ultrasonic inspection, welding inspection
equipment, fault detection, thickness measurement or flow measurement require knowledge and experience in the
handling and analysis of the measurement data obtained.
PCE Instruments offers training courses on this
subject, either at our branch or directly at the customer premises. These courses are specially designed to
familiarize the client with the management of the inspection teams and show him the first steps in the
analysis of data or images.
Duration: Usually 4 hours (2 hours of theory on the device and 2
hours of practical exercises).
Date: By individual agreement.
Formalities: Participants
are expected to have a basic knowledge of the corresponding subject.